How a custom-built digital shop floor optimises critical processes for a leading airline
17 December 2024 • Use Case
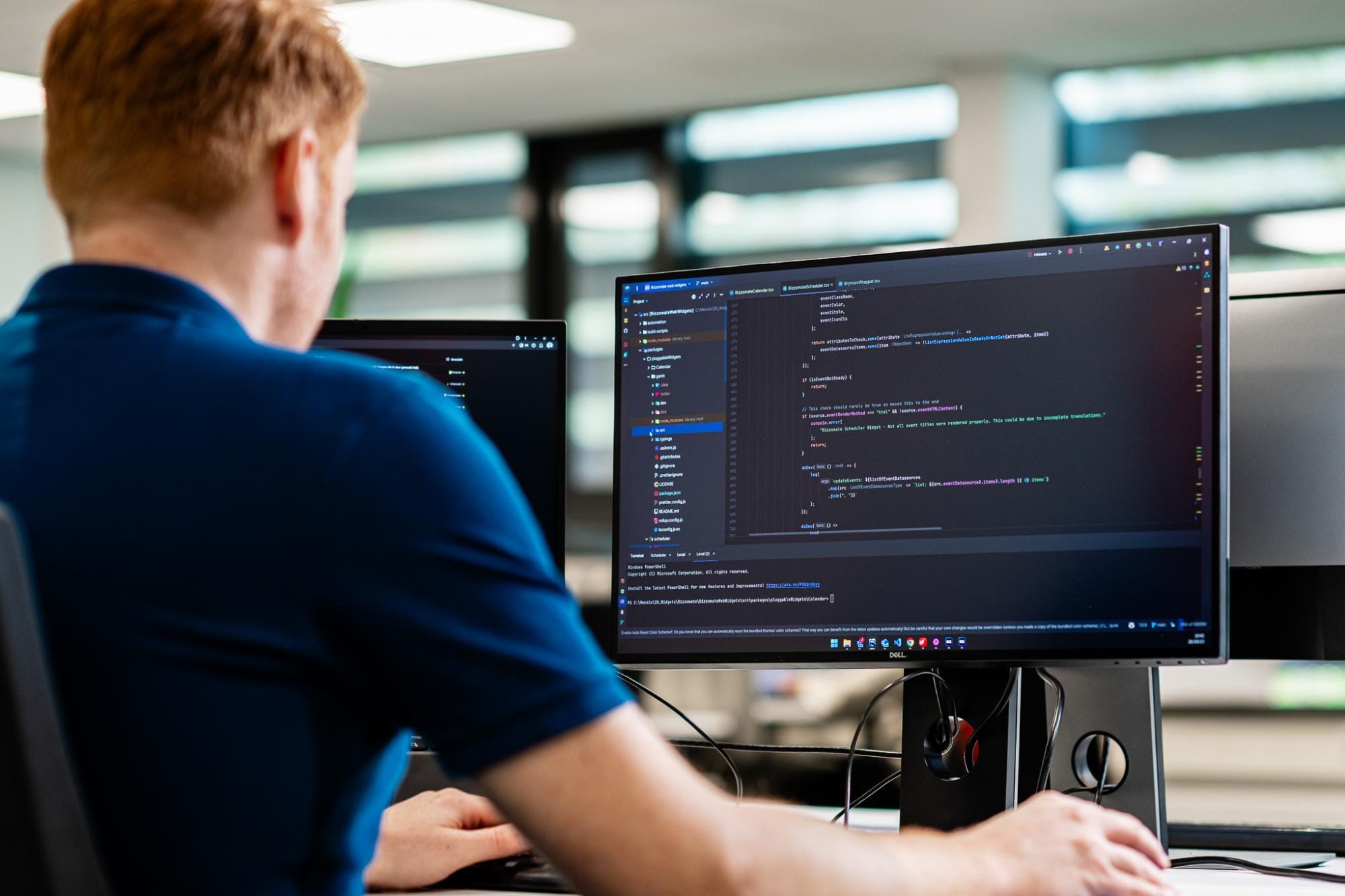
KLM accelerates efficiency with robotic process automation
KLM, one of the world’s oldest and most respected airlines, has been delivering memorable travel experiences since 1919. Serving millions of passengers annually, the company continuously expands, requiring a strong focus on the speed, precision, and scalability of its business processes. Recognising that scaling Robotic Process Automation (RPA) is key to meeting customer and employee needs, KLM partnered with Ciphix on this transformative initiative.
KLM engaged Ciphix, alongside the KLM Digital Studio, to streamline the process of exchanging aircraft parts that require cleaning or maintenance via the aeroexchange.com platform. As order volumes increased, this essential task—critical to keeping more than 200 aircraft in top condition—became increasingly time-consuming and error-prone. Exchanging parts involves performing repetitive tasks with speed and accuracy, a significant burden for human employees but an ideal task for a digital workforce.
By automating key parts of this process, KLM aimed to reduce the time per part from one hour to just 15 minutes. This ambitious goal was exactly the type of challenge Ciphix thrives on. Equipped with the tools to design and implement a fully customised RPA solution, Ciphix was ready to take action.
What we built
The project began with a comprehensive analysis of KLM’s part exchange process to identify the best automation opportunities. By mapping the “as-is” process—the manual workflow before RPA implementation—we pinpointed several tasks that software robots could take over. With a clear strategy in place, we set out to deliver the most tailored and effective solution for KLM.
Using UiPath combined with custom development, Ciphix created a digital shop floor of advanced software robots, each designed to boost efficiency while minimising human effort. These robots now manage multiple stages of the exchange process. When a new order is placed, a robot generates a return label for the customer to ship the part. Upon arrival, other robots scan barcodes and process the part through a terminal application to update history and financial records.
Our RPA solution also validates customer-supplied data, providing KLM with valuable insights into the process. As each robot logs and reports all statuses, human operators maintain full control and visibility, enabling continuous process improvements.
The impact
For nearly six months, Ciphix’s software robots have been working seamlessly within KLM Royal Dutch Airlines, handling tasks previously performed manually. This scalable digital shop floor significantly reduces time and costs while allowing employees to focus on more valuable and engaging work.
Having already delivered substantial results, Ciphix has been invited to optimise additional areas of KLM’s business processes, working closely with KLM’s digital transformation teams. This ongoing collaboration strengthens both organisations, making it even easier for KLM to elevate safety, efficiency, and exceptional service to new heights.
We will help you further!
Replace outdated systems, digitize complex business processes and accelerate innovation.